Today we are going to meet Tran The Hung, our Cleanroom Engineering Expert at Archetype Vietnam. With over 14 years of experience, he specializes in designing high-performance cleanroom environments for industries such as pharmaceuticals, food and beverages, and healthcare
In this edition, we explore the science behind cleanroom design, focusing on the technical complexities and challenges involved in creating and maintaining contamination-free environments that meet the highest standards of safety, efficiency, and reliability.
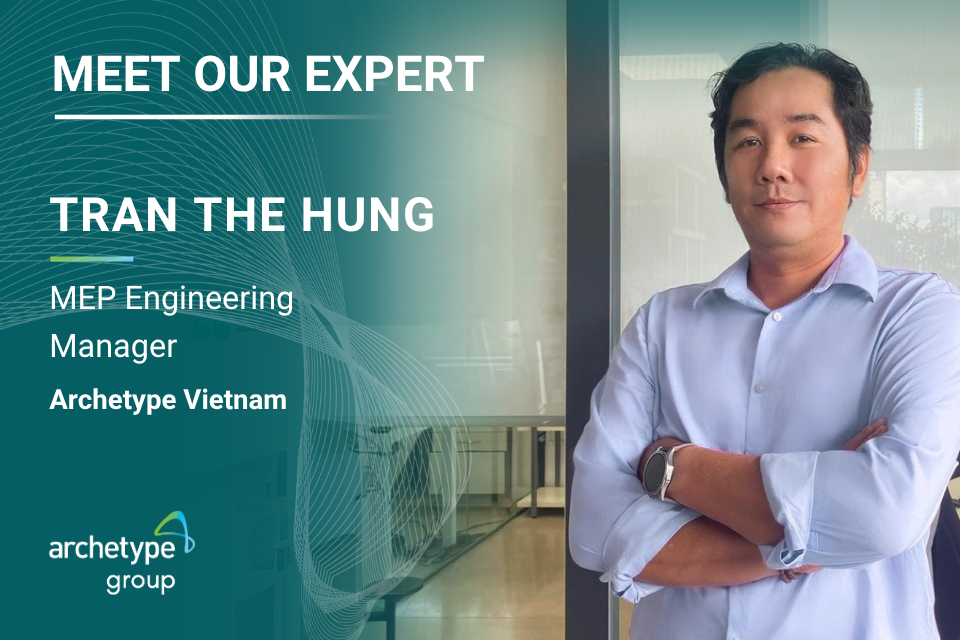
As a cleanroom engineering expert, you’ve worked on a variety of high-standard projects across industries. To start, could you share which international standards or guidelines you frequently work with beyond ISO 14644?
While ISO 14644 forms the foundational framework for cleanroom classifications, it is far from the only standard guiding our work. Depending on the project type and location, we also work with:
- WHO GMP (Good Manufacturing Practices): Governs global pharmaceutical production, especially in pharmaceutical and biotechnology projects.
- EU GMP Annex: Sets out detailed guidelines for the manufacture of sterile medicinal products.
- PICS GMP: Harmonizes GMP compliance requirements across multiple countries and regulatory bodies.
- HACCP (Hazard Analysis and Critical Control Points): A widely used risk management standard in the food and beverage industry.
- FDA cGMP (21 CFR Part 210 and 211): Critical for US-based pharmaceutical projects, ensuring compliance with US regulations.
- VDI 2083: A German engineering standard providing technical guidance on air cleanliness, particle control, and performance benchmarks in cleanrooms.
- JACA B 9920: A Japanese cleanroom standard issued by the Japanese Air Cleaning Association, tailored to local industry needs.
For industries that rely on cleanrooms, contamination control is critical. What are the biggest risks of improper cleanroom design or maintenance?
The risks of poor cleanroom design or maintenance can be severe ranging from product contamination and regulatory non-compliance to operational downtime and financial loss. One of the most common mistakes is failing to understand the process requirements. A cleanroom design must reflect its intended purpose, cleanliness classification, and operational parameters, including air change rates, temperature and humidity control, and pressure zoning.
Non-compliance with regulatory standards is another major risk. Whether it’s ISO, EU GMP, FDA, or other regional standards, staying current and compliant is non-negotiable. Involving a multidisciplinary team, especially experienced HVAC engineers, ensures that air filtration and circulation systems are properly designed and maintained. This includes the use of HEPA filters and careful airflow pattern planning.
Inadequate pressure control can compromise the entire system. Cleanrooms must maintain precise pressure differentials to prevent contamination flow between zones. We recommend integrating adjustable pressure control systems with gauges and alarms for real-time monitoring and regularly testing them to maintain integrity.
Material choice also carries a risk. Cleanrooms require non-porous, easy-to-clean, chemical-resistant materials such as stainless steel. Selecting cheaper or less suitable materials might seem like a short-term saving, but it often leads to long-term contamination problems and higher remediation costs.
Finally, it’s important not to underestimate project costs. Cleanrooms involve specialized materials and systems that require accurate forecasting. Budgeting must include HVAC, filtration, finishes, and ongoing maintenance. We always recommend allocating a contingency fund for unexpected challenges and aligning cost projections with input from experienced architects, engineers, and quality surveyors.
How do you balance meeting strict contamination control requirements while ensuring the cleanroom remains efficient and cost-effective for clients?
Cleanrooms are inherently energy-intensive due to the high demands for air filtration, pressure control, and environmental stability. However, by integrating smart design principles and advanced technologies, we can significantly improve efficiency without compromising performance.
One of the most effective approaches is optimizing air change rates (ACR). For example, using dynamic airflow control systems like VAV (Variable Air Volume), DCV (Demand-Controlled Ventilation), and smart Building Management Systems (BMS) allows us to adjust airflow in real time based on zone requirements. We also implement pressure cascade zoning, enabling us to reduce air change rates in less critical areas while maintaining overall cleanliness.
Another strategy is the use of high-efficiency filtration systems. HEPA and ULPA filters with low pressure drop help lower fan energy consumption. It’s crucial to schedule regular maintenance and replacement to prevent overloads on air handling units (AHUs). Additionally, Fan Filter Units (FFUs) with variable-speed fans can adjust energy use based on real-time needs.
Smart HVAC and climate control are other major factors. We utilize energy recovery systems like heat exchangers to capture and reuse energy from exhaust air. Desiccant dehumidification systems help reduce cooling loads, and Chiller Plant Management Systems, integrated into BMS platforms, enhance automation and efficiency. In more advanced cases, we are beginning to explore AI-driven HVAC systems, although these are not yet widely adopted in Vietnam.
We also focus on equipment and lighting efficiency—installing high-efficiency motors, Variable Frequency Drives (VFDs), and automated power management systems. Switching to LED lighting with motion sensors has proven to be both energy- and cost-efficient.
Water usage is another consideration in cleanroom environments. We promote water recycling systems using ultrapure water (UPW) for rinsing and cleaning processes. Low-flow fixtures and real-time monitoring help detect leaks and optimize usage, supporting both operational sustainability and cost management.
If you had to highlight one key lesson learned from projects that you have worked on, what would it be?
If I had to highlight one key lesson based on several projects I’ve worked on, such as ACE Project and the Medochemie Factory, it would be the importance of early and thorough coordination across all disciplines, from MEPF to Process Engineering, Architecture, and Civil. Establishing a dedicated coordination meeting at the beginning of the project ensures that all technical and regulatory requirements are fully understood and properly integrated from the outset.
Late changes such as resizing MEP shafts or relocating airlocks can trigger major design revisions and increase costs significantly. It is essential to gather all client inputs and clearly understand the project scope and applicable standards before moving into detailed design. Misinterpreting or applying the wrong standard can be a costly mistake. For instance, delivering a cleanroom designed to ISO 14644 standards when the client requires EU GMP compliance could lead to regulatory rejection.
Other recurring issues include HVAC and pressure control failures, specifically inadequate cascading pressure that can allow cross-contamination in sterile areas, and inappropriate material selection. Using painted gypsum walls instead of FRP or stainless steel in high-grade cleanroom areas can pose serious contamination risks. even details like pipe insulation materials matter; the wrong material can lead to microbial growth or particle shedding.